What is Porosity in Welding: Typical Sources and Efficient Treatments
What is Porosity in Welding: Typical Sources and Efficient Treatments
Blog Article
Porosity in Welding: Identifying Common Issues and Implementing Best Practices for Prevention
Porosity in welding is a prevalent concern that commonly goes unnoticed up until it creates substantial issues with the integrity of welds. This typical issue can jeopardize the strength and toughness of bonded frameworks, positioning safety and security dangers and causing pricey rework. By understanding the origin causes of porosity and executing reliable avoidance strategies, welders can substantially boost the quality and reliability of their welds. In this conversation, we will certainly check out the vital elements adding to porosity development, analyze its detrimental effects on weld performance, and go over the very best practices that can be adopted to minimize porosity occurrence in welding procedures.
Usual Reasons For Porosity

One more constant perpetrator behind porosity is the existence of contaminants externally of the base metal, such as oil, grease, or corrosion. When these pollutants are not efficiently removed prior to welding, they can evaporate and come to be trapped in the weld, causing flaws. Utilizing filthy or damp filler materials can present impurities into the weld, adding to porosity concerns. To minimize these typical root causes of porosity, extensive cleansing of base metals, proper protecting gas selection, and adherence to optimal welding parameters are important methods in achieving top quality, porosity-free welds.
Impact of Porosity on Weld Quality

The existence of porosity in welding can substantially endanger the structural stability and mechanical residential properties of bonded joints. Porosity creates spaces within the weld steel, deteriorating its total strength and load-bearing capability. These gaps serve as tension focus factors, making the weld more at risk to breaking and failure under applied lots. Additionally, porosity can decrease the weld's resistance to rust and various other ecological aspects, additionally lessening its long life and performance.
Welds with high porosity degrees often tend to show lower effect strength and minimized ability to warp plastically prior to fracturing. Porosity can restrain the weld's capability to effectively send forces, leading to early weld failing and potential security click this threats in critical frameworks.
Ideal Practices for Porosity Prevention
To boost the architectural integrity and high quality of welded joints, what certain steps can be carried out to decrease the occurrence of porosity during the welding procedure? Using the correct welding technique for the particular material being welded, such as readjusting the welding angle and weapon setting, can better stop porosity. Routine evaluation of welds and immediate removal of any type of problems recognized during the welding process are necessary practices to stop porosity and generate top quality welds.
Significance of Appropriate Welding Strategies
Executing proper welding techniques is paramount in guaranteeing the architectural integrity and top quality of welded joints, building upon the structure of reliable porosity avoidance steps. Welding strategies directly impact the general toughness and durability of the bonded structure. One key element of correct welding strategies is keeping the right warmth input. Extreme heat can lead to increased porosity as a result of the entrapment of gases in the weld swimming pool. On the other hand, not enough heat may result in insufficient fusion, producing possible weak points in the joint. In addition, making use of the suitable welding parameters, such as voltage, present, and travel rate, is essential for attaining audio welds with minimal porosity.
Moreover, the option of welding process, whether it be MIG, TIG, or stick welding, should straighten with the details demands of the project to make certain ideal outcomes. Appropriate cleansing Click This Link and preparation of the base steel, along with selecting the appropriate filler material, are also vital components of competent welding techniques. By sticking to these ideal practices, welders can decrease the risk of porosity development and create premium, structurally sound welds.
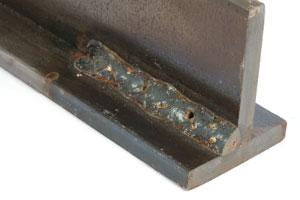
Checking and Quality Control Actions
Checking treatments are essential to discover and prevent porosity in welding, making certain the strength and durability of the last product. Non-destructive screening approaches such as ultrasonic testing, radiographic testing, and aesthetic examination are generally utilized to identify prospective defects like porosity.
Carrying out pre-weld and post-weld assessments is likewise important in maintaining quality control requirements. Pre-weld examinations involve confirming the materials, equipment setups, and tidiness of the workplace to stop contamination. Post-weld examinations, on the various other hand, examine the final weld for any type of problems, consisting of porosity, and confirm that it meets defined criteria. Applying a thorough top quality control strategy that includes extensive screening procedures and evaluations is vital to lowering porosity issues and making certain the general quality of bonded joints.
Conclusion
Finally, porosity in welding can be a common concern visit this website that impacts the top quality of welds. By determining the common root causes of porosity and carrying out ideal techniques for prevention, such as proper welding techniques and screening actions, welders can ensure excellent quality and trusted welds. It is important to prioritize prevention methods to decrease the event of porosity and preserve the stability of welded structures.
Report this page